3D printers: Difference between revisions
No edit summary |
(Initial integration of Eiffel page.) |
||
Line 2: | Line 2: | ||
=Challenges= | =Challenges= | ||
Subtractive manufacturing can produce many goods - particularly with multi-step production processes and multiple parts. But some objects can't be made that way. Others are simpler and faster to manufacture in a single operation additively. | Subtractive manufacturing can produce many goods - particularly with multi-step production processes and multiple parts. But some objects can't be made that way. Others are simpler and faster to manufacture in a single operation additively. | ||
==Chatter== | |||
We need to turn this into a machine with a stationary bed and mobile gantry if we're to extend it into use as a powder printer. | |||
This is conceptually straightforward, if we can do a dropping bed and borrow [[candyfab]]'s or someone else's powder mechanisms. | |||
=Approaches= | =Approaches= | ||
Line 19: | Line 22: | ||
| 1 || [https://mahor.xyz/ Mahor pellet hot end] || [https://mahor.xyz mahor.xyz] | | 1 || [https://mahor.xyz/ Mahor pellet hot end] || [https://mahor.xyz mahor.xyz] | ||
|} | |} | ||
==Structure== | |||
===Beam=== | |||
1x1 inch, cost ~$22 per 6ft piece. | |||
''The preliminary concept sketch seems to show (very roughly) about 32 feet of beam, requiring 6 of these 6 ft pieces.'' | |||
''The photos seem to show (very roughly) about 16 feet of beam, requiring 3 of those 6 ft pieces -- is that really all that is required, or were those photos taken halfway through construction?'' | |||
square steel tubing or square wood beams. | |||
If possible, these are perforated and otherwise shaped using the mom-Eiffel, or a handy drill press. | |||
==Lots of PegBoard== | |||
See [[LeCorb]]. | |||
==Rails== | |||
Highly variable. | |||
Drawer slides are easy to prototype with. | |||
Real steel rod for when we're serious. | |||
==Motion Control== | |||
[[:category: DriveTrains#rotary to linear motion conversion | rotary to linear motion conversion]]: | |||
Undecided: | |||
Toothed [[Belt]], Threaded Rod, or Rack and Pinion | |||
==Cross-Connectors, Fasteners== | |||
3D printed by the 'Mom' Eiffel or RepRap, or made by cnc router, | |||
or laser cutter. | |||
''Huh? Once you put the 3 bolts through the tri-lap joint, and tighten the nut against the washers, what other connector or fastener do you need?'' | |||
===Material=== | |||
*[[Thermoplastic]] or | |||
*[[Filled_Epoxy]] (Using a CNC router and a 3D printer to make the molds | |||
for the fittings, and then using the molds to cast fittings from filled epoxy.) | |||
==Spindel== | |||
*Taig Spindle | |||
or | |||
http://www.engravingmachine.com/html/router_spindles.html | |||
e.g. | |||
http://www.engravingmachine.com/html/router_spindles_-_kress.html | |||
=Workflows= | =Workflows= | ||
Line 42: | Line 87: | ||
<youtube>rp3r921DBGI</youtube> | <youtube>rp3r921DBGI</youtube> | ||
<youtube>nRLJ4ylGTFc</youtube> | <youtube>nRLJ4ylGTFc</youtube> | ||
{{Development | |||
|image = Eiffel_Concept.jpg | |||
|description = a powder printer with a stationary bed and mobile gantry | |||
|status = Concept | |||
|author = Sebastien Bailard, timschmidt | |||
|categories = {{tag|CNC Mill}}, {{tag|CNCmachine}}, {{tag|powder}} | |||
|reprap = Post-Mendel | |||
}} | |||
=Introduction= | |||
[[File:Eiffel_01.jpg|right|400px|This is 400 pixels wide, and on the left.]]<br> | |||
[[File:Eiffel_02.jpg|right|400px|This is 400 pixels wide, and on the left.]]<br> | |||
[[File:Eiffel_04.jpg|right|400px|This is 400 pixels wide, and on the left.]]<br> | |||
[[File:Eiffel_05.jpg|right|400px|This is 400 pixels wide, and on the left.]]<br> | |||
[[File:Eiffel_06.jpg|right|400px|This is 400 pixels wide, and on the left.]] | |||
Eiffel is a proposal for a post-[[Mendel]] [[RepRap]], which will function as a 3D printer, and as a [[CNC_Router]]. | |||
[[File:Eiffel_Concept.jpg|frame|center|This is a preliminary concept sketch. (The beams should have through-holes repeating along the side.)]] | |||
The first version will have a footprint of ~1 ft x 2 ft (30 cm x 60 cm), and a workspace of | |||
8.5 inch x 11 inch x 4 inch, or 20 cm x 30 cm x 10 cm. | |||
Eiffel is made from a number of square beams bolted | |||
toghether in [[TriLap]] joints. These square beams are either steel tube, | |||
aluminum tube, or solid wood, depending on availability and user | |||
preference. The beams are drilled for bolting together in tri-joints. | |||
If convenient, these beams are drilled with regularly spaced | |||
through-holes along each long side. (See [[RBS]]). | |||
We aim to supersede [[Mendel]] by being able to engrave and drill [[Automated Circuitry Making | pcbs]], | |||
and also machine wood and non-ferrous metals. Eiffel will also be | |||
useful for [[hybrid]] fabrication. This is essential for making [[RBS/Gears|Gears]]. | |||
=Files/Modeling= | |||
Eiffel is still in preliminary development. We currently have the 'napkin-sketch' above, a [[Blender]] file or two (available tomorrow), and a number of graph paper sketches. | |||
Please use your favorite modeling program or CAD program and join in! | |||
=Applications= | |||
*Drilling steel or aluminum beams for daughter-Eiffels. (We may have to set up in a [[CNC_Mill]] configuration to drill steel. | |||
*PCB routing | |||
*Hobby-scale Robot parts (CNC-routed and 3D printed) | |||
User wants and needs: Journeyman (just graduated) | |||
architecture student, who will need CNC router/3D printer for | |||
modelmaking and crafting. | |||
Also: FabLabs, RepRap users, hobbyists (RC plane folk cut a lot of | |||
balsa on medium scale CNC routers) and educators. | |||
=Design Philosophy= | |||
The RepRap project has successfully made a 3D printer | |||
using the [[GPL]] for a license. Eiffel will do the same, and will | |||
leverage and contribute to RepRap technology and community. We will | |||
use the GPL and the RepRap website to be able to freely interoperate with | |||
standard RepRap hardware and software. | |||
There is no mature and well-publicized GPL CNC router. Eiffel | |||
will fill that space, along with being a CNC-router. | |||
=Working Notes= | |||
Everything below here is poorly organized. Sorry. | |||
'''Capabilities''' | |||
*Work volume of 24" x 48" x 8". | |||
*Wood cutting - ~100% duty cycle. | |||
*Metal cutting - light aluminum and other non-ferrous cutting. | |||
*Steel - drilling. | |||
*3D printing: | |||
1) Thermoplastic: like a normal RepRap | |||
2) Powder Printer: Preliminary discussion. | |||
http://dev.forums.reprap.org/read.php?1,31168,31181 | |||
=Fabrication/Tooling= | |||
To make an eiffel from square tubing or beam, drilled for bolting together in tri-joints. It | |||
will _not_ require a normal machine shop. | |||
==Saw== | |||
==Drill Press== | |||
== ??? == | |||
Maybe benchtop CNC mill for fittings, but would greatly prefer having mother Eiffel | |||
or other cnc router, 3D printer make fittings from [[Filled_Epoxy]]. | |||
== Self-replication == | |||
'''Does it drill holes in the beams of it's daughter machines?''' You | |||
can. | |||
But for the first one, it's much much faster to source pre-drilled | |||
square steel beams. McMaster-Carr down in the US has it, and local | |||
construction suppliers _everywhere_ should be able source it given 2 | |||
months forewarning. | |||
http://www.mcmaster.com/#steel-structural-tubing/=49tu63 | |||
Once you've got a machine, it's really easy to make lots of wood grid | |||
beam. And maybe you can drill holes in steel with it. It would be | |||
convenient, and a useful target benchmark. It would be hard to make | |||
this as good as a [[Taig Mill]], but fun to try. | |||
== normal CNC routing == | |||
'''How do we generate G-Code from for cutting the outsides of | |||
stuff. You know, 80% of normal CNC routing?''' | |||
Perhaps use one of the "2D" packages listed at [[Useful Software Packages]], | |||
and if it doesn't directly produce G-code, use something like [[Builders/Replath]] | |||
to convert from SVG or DXF to G-code? | |||
[[Category:MillStrap]] | |||
[[category:steel]] | |||
[[category:Multi-Material]] | |||
[[category:Non-Metric]] | |||
[[category:powder]] | |||
[[category:RBS]] | |||
[[category:working developments]] | |||
[[category:CNC Mill]] | |||
[[category:CNC Router]] | |||
[[Category: Projects]] | [[Category: Projects]] | ||
[[Category: Manufacturing]] | [[Category: Manufacturing]] |
Revision as of 02:03, 3 February 2021

Challenges
Subtractive manufacturing can produce many goods - particularly with multi-step production processes and multiple parts. But some objects can't be made that way. Others are simpler and faster to manufacture in a single operation additively.
Chatter
We need to turn this into a machine with a stationary bed and mobile gantry if we're to extend it into use as a powder printer. This is conceptually straightforward, if we can do a dropping bed and borrow candyfab's or someone else's powder mechanisms.
Approaches
Use linear bearings, motors, and a controller to build a 3D printer. A hotend designed to consume plastic pellets instead of filament allows for direct recycling of shredded plastic goods.
Polymer recycling codes for distributed manufacturing with 3-D printers
Tools
Parts
Quantity | Part | Link |
---|---|---|
1 | Mahor pellet hot end | mahor.xyz |
Structure
Beam
1x1 inch, cost ~$22 per 6ft piece.
The preliminary concept sketch seems to show (very roughly) about 32 feet of beam, requiring 6 of these 6 ft pieces.
The photos seem to show (very roughly) about 16 feet of beam, requiring 3 of those 6 ft pieces -- is that really all that is required, or were those photos taken halfway through construction?
square steel tubing or square wood beams.
If possible, these are perforated and otherwise shaped using the mom-Eiffel, or a handy drill press.
Lots of PegBoard
See LeCorb.
Rails
Highly variable.
Drawer slides are easy to prototype with. Real steel rod for when we're serious.
Motion Control
rotary to linear motion conversion:
Undecided: Toothed Belt, Threaded Rod, or Rack and Pinion
Cross-Connectors, Fasteners
3D printed by the 'Mom' Eiffel or RepRap, or made by cnc router, or laser cutter. Huh? Once you put the 3 bolts through the tri-lap joint, and tighten the nut against the washers, what other connector or fastener do you need?
Material
- Thermoplastic or
- Filled_Epoxy (Using a CNC router and a 3D printer to make the molds
for the fittings, and then using the molds to cast fittings from filled epoxy.)
Spindel
- Taig Spindle
or http://www.engravingmachine.com/html/router_spindles.html e.g. http://www.engravingmachine.com/html/router_spindles_-_kress.html
Workflows
Development targets
Repositories of printable parts
References
Introduction
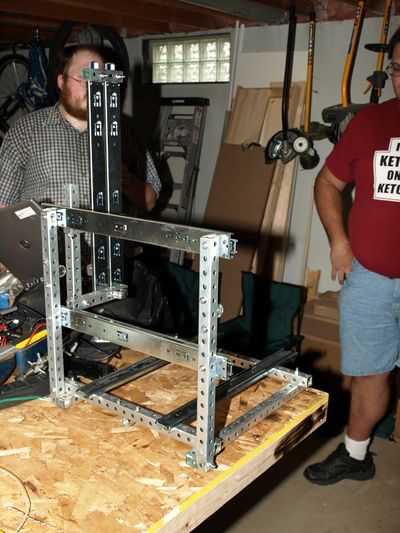
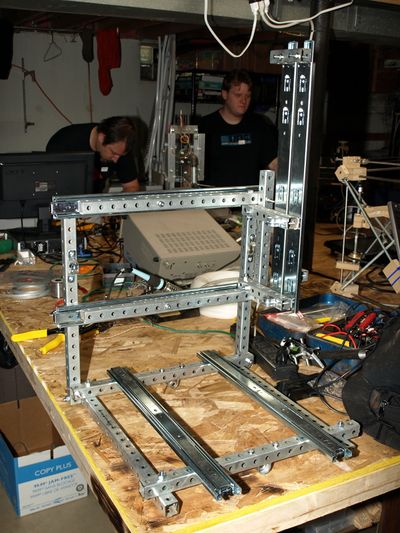
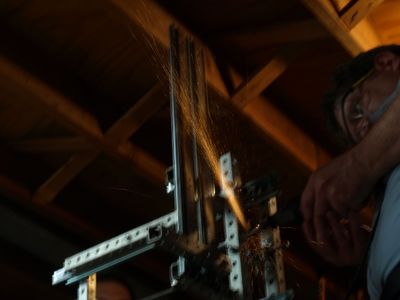
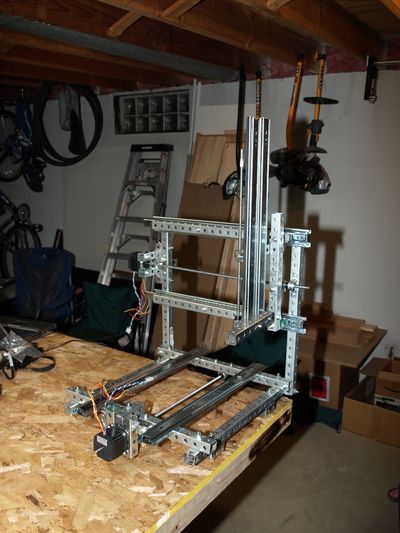
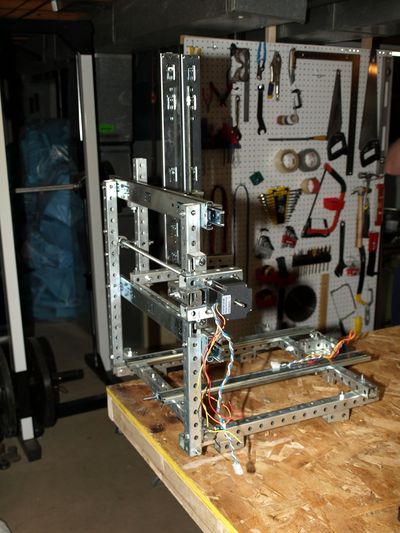
Eiffel is a proposal for a post-Mendel RepRap, which will function as a 3D printer, and as a CNC_Router.
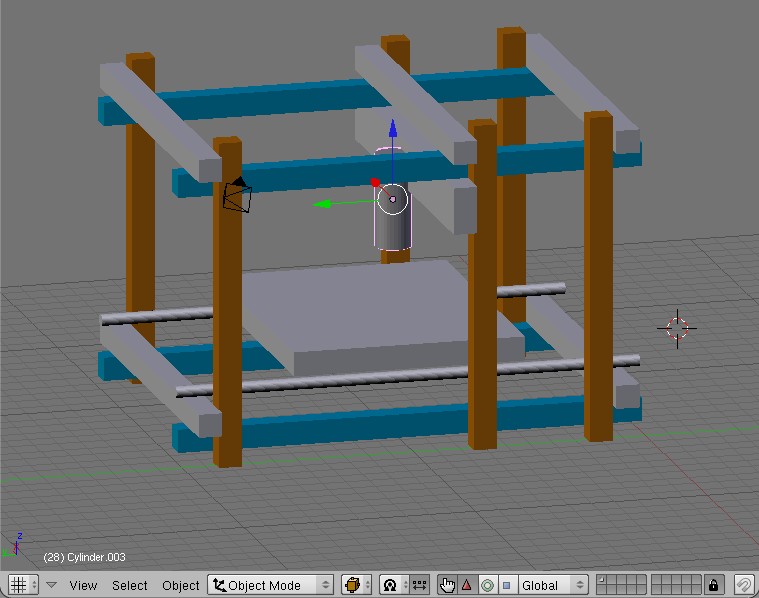
The first version will have a footprint of ~1 ft x 2 ft (30 cm x 60 cm), and a workspace of 8.5 inch x 11 inch x 4 inch, or 20 cm x 30 cm x 10 cm.
Eiffel is made from a number of square beams bolted toghether in TriLap joints. These square beams are either steel tube, aluminum tube, or solid wood, depending on availability and user preference. The beams are drilled for bolting together in tri-joints. If convenient, these beams are drilled with regularly spaced through-holes along each long side. (See RBS).
We aim to supersede Mendel by being able to engrave and drill pcbs, and also machine wood and non-ferrous metals. Eiffel will also be useful for hybrid fabrication. This is essential for making Gears.
Files/Modeling
Eiffel is still in preliminary development. We currently have the 'napkin-sketch' above, a Blender file or two (available tomorrow), and a number of graph paper sketches.
Please use your favorite modeling program or CAD program and join in!
Applications
- Drilling steel or aluminum beams for daughter-Eiffels. (We may have to set up in a CNC_Mill configuration to drill steel.
- PCB routing
- Hobby-scale Robot parts (CNC-routed and 3D printed)
User wants and needs: Journeyman (just graduated) architecture student, who will need CNC router/3D printer for modelmaking and crafting.
Also: FabLabs, RepRap users, hobbyists (RC plane folk cut a lot of balsa on medium scale CNC routers) and educators.
Design Philosophy
The RepRap project has successfully made a 3D printer using the GPL for a license. Eiffel will do the same, and will leverage and contribute to RepRap technology and community. We will use the GPL and the RepRap website to be able to freely interoperate with standard RepRap hardware and software.
There is no mature and well-publicized GPL CNC router. Eiffel will fill that space, along with being a CNC-router.
Working Notes
Everything below here is poorly organized. Sorry.
Capabilities
- Work volume of 24" x 48" x 8".
- Wood cutting - ~100% duty cycle.
- Metal cutting - light aluminum and other non-ferrous cutting.
- Steel - drilling.
- 3D printing:
1) Thermoplastic: like a normal RepRap
2) Powder Printer: Preliminary discussion. http://dev.forums.reprap.org/read.php?1,31168,31181
Fabrication/Tooling
To make an eiffel from square tubing or beam, drilled for bolting together in tri-joints. It will _not_ require a normal machine shop.
Saw
Drill Press
???
Maybe benchtop CNC mill for fittings, but would greatly prefer having mother Eiffel or other cnc router, 3D printer make fittings from Filled_Epoxy.
Self-replication
Does it drill holes in the beams of it's daughter machines? You can.
But for the first one, it's much much faster to source pre-drilled square steel beams. McMaster-Carr down in the US has it, and local construction suppliers _everywhere_ should be able source it given 2 months forewarning. http://www.mcmaster.com/#steel-structural-tubing/=49tu63
Once you've got a machine, it's really easy to make lots of wood grid beam. And maybe you can drill holes in steel with it. It would be convenient, and a useful target benchmark. It would be hard to make this as good as a Taig Mill, but fun to try.
normal CNC routing
How do we generate G-Code from for cutting the outsides of stuff. You know, 80% of normal CNC routing?
Perhaps use one of the "2D" packages listed at Useful Software Packages, and if it doesn't directly produce G-code, use something like Builders/Replath to convert from SVG or DXF to G-code?